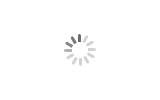
High pressure die Casting Machine 1300 ton
Brand :RUIDA
Product origin :China
Delivery time :30 Days
Horizontal cold chamber die casting machine is one of our series machines, mainly used in automotive, motorcycle, gas, aviation, electrician, electronic equipment, toys, decoration and computer industries, for aluminum, zinc, magnesium, copper, etc. Production of non-ferrous alloy castings. (The melting point of zinc alloy is about 420 °C, the melting point of aluminum alloy is about 660 °C, the melting point of magnesium alloy is about 650 °C, and the melting point of copper alloy is about 1100 °C).
Cold Chamber Die Casting Machine RDC1300
Spheroidal graphite cast iron mould board, high tensile alloy steel bar, and high-abrasive chromium plating.
Mould control under multi-level pressure and speed, intelligent mould protection against low pressure.
C-shaped or H-shaped crossbeam linked with pillar support to ensure high reliability and precision of material stamping.
Hydraulic gear-type adjusting device.
High-speed ejection and core pulling device.
Independent piston-type supercharger
Accumulator with two speed levels ensuring
Fast and stable injection.
High Tensile Clamping System.
a. Spheroidal graphite cast iron mould board and reamer processed by high precision CNC machining center ensure high precision and solidity of mould clamping system.
b. Dual toggle and five pivots ensure the stable and smooth movement of mould board.
c. Wide space between four draw bars and long stroke for mould with large sizes.
d. Adjust mould board by finite-element analysis for the purpose of even stress, low risk of deformation and high-precision of mould clamping.
Ejector adopts special design for adjustable stroke.
Water-cooling oil circuit cooler ensures constant pressure and viscosity of oil.
Hydraulic gear-type adjusting device is easy to use and ensures accurate mould thickness.
Imported clamping force testing device ensures accurate adjustment of clamping force.
Specifications
Facility
Features
Electronic control unit
1. In this design, this series of models fully considers various die-casting processes, and sets up single-machine manual and semi-automatic, and can also be equipped with die-casting auxiliary machines (such as ladle, sprayer, extractor, etc.) to realize automatic die-casting system.
2. This series of models has the characteristics of advanced design, excellent production, good performance, fast speed and low energy consumption. All its operating procedures are concentrated in computer control, make it easy to operate, stable in performance, safe and reliable.
3. The standard model oil pump is equipped with electric proportional control of the flow of the hydraulic system, with multistage pressure and speed control and low-pressure mold clamping protection.
4, using Omron PLC control system, human-computer interface (touch screen), stable and reliable operation, high control accuracy, production management, fault diagnosis and mold parameter storage, central electric lubrication system, stable and reliable.
Oil section
1. The injection speed is divided into four levels of proportional control, independent fast and supercharged energy storage device. The opening and closing mode adopts proximity switch or electronic ruler detection control, which is convenient for adjustment and accurate control.
2, excellent injection performance: carefully developed patented injection system, the oil circuit is more concise, the fault is lower (basically zero fault), the injection is fast and stable, the pressure build time is faster than the competitors 5 times or more, currently The pressure-building time of the competitors is 150-250ms, we keep it at 20-30ms, the floating rate of change is reduced, the customer yield is greatly improved, and the output ratio of the equipment is improved. (As the product gradually cools, the faster the build time, the higher the yield, patent number 201420521462.3).
3. In order to improve safety, manual unloading valves are provided for the injection oil passages of all models, which is convenient for maintenance and repair.
4. The smooth operation of the oil circuit of the machine and the service life of the hydraulic components are the cleanliness of the pressure oil. In order to ensure the cleanliness of the oil circuit, the Ruida die-casting machine maintains good cleaning in the manufacturing process, and is also in the oil inlet of the fuel tank. The oil inlet has been specially designed, and the oil inlet is 4cm high to ensure that the waste water and waste oil flow do not enter the oil tank.
5.Our die casting machine,Using high performance, Low noise dual-blade pump, which is durable, energy saving and with high efficiency.
6.The oil circuit cooling uses a new generation of interposer coolers, which is more efficient than the previous generation of external coolers, which can effectively reduce the oil temperature and make the seals and hydraulic components last longer.
7. Quick hydraulic ejector and core-pulling device, with the function of extracting the upper guide column on the operating side, the mold exchange is convenient and fast. (RDC1000 and above models tie bar puller optional).
Clamping Unit
1. The ultra-rigid clamping mechanism independently designed by Ruida is adopted. After elements analysis and extensive practice, due to the addition of strong struts, the structure has a smooth and easy mode adjustment and a smooth opening and closing mode. (Most other brands machine in the market,while open and close the mold, the tail plate is easy to jump up and down, and the mold adjustment is easy to get stuck).
2. In order to save the customer's maintenance costs, small and medium models use split machine toggles (RDC160, RDC200, RDC230, RDC330, RDC400). Due to the dust and the poor working environment, after several years, the wear of the lock-opening system still torture the die casting manufacturers, the cost of the joint-type maintenance is high, and the repair time is long. Our company uses the split toggles for quick and convenient maintenance. , completely solved such problems.
3. The machine toggles of RDC330 and above is reinforced, and its rigidity is increased by 40-50%, which ensures greater clamping force and reduces the flash of the molten metal during the production process.
4. The wide range of self-lubricating carbon-containing bearings improves the lubrication effect of the moving parts, and the movement of the machine is smoother and smoother. It is more reliable and has a longer life than ordinary copper sleeves. Part of positions is maintenance-free, greatly improving production efficiency. Reduce the use of grease and reduce the production cost of die casting. The use environment is cleaner and greener.
5. All copper sleeve steel division adopts ultra-low temperature refrigeration assembly, which can enhance the bonding force with the casting and improve the service life of the lock opening mold system.
6. The honeycomb platen structure expands the use space without affecting its strength, and at the same time makes the appearance more compact and beautiful.
7. The die casting quality and the span life of the machine are very serious due to the vibration and temperature rise, especially the temperature of the die-cast aluminum reaches 710 ° C, and the temperature of the die-cast brass reaches 1100 ° C, the chamber and The fix platen of the machine are connected together, and the chamber transfers heat to the fix platen. After a long period of continuous high temperature, the deformation of the fix platen and the aging of the material result, which affects the quality of the die-casting product and reduces the service life of the machine. Our all cold chamber die casting machines, in order to control the temperature influence,installed a cooling system. The 400T and above models are mainly due to the large heat generation. A large flow cooling system is installed.