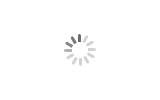
200/300/400Ton Hot Chamber Die Casting Machine
Brand :Daseon
Product origin :China
Delivery time :30 Days
The Smart Casting Machine merges cutting-edge automation with user-friendly design, lowering operational complexity while maximizing safety and flexibility.
The Automated High-Pressure Casting System redefines modern manufacturing by merging advanced automation, operator safety, and flexible configurations. Designed for industries requiring rapid adaptability—such as automotive, aerospace, and consumer electronics—this system streamlines workflows while ensuring precision and compliance with global standards. Below, we explore its technological innovations, user-centric design, and real-world impact.
1. Advanced Automation for Precision Manufacturing
The Automated High-Pressure Casting System leverages cutting-edge technology to minimize human intervention and maximize repeatability.
Unified Control Interface:
A touchscreen provides intuitive access to all parameters, supporting multiple languages for global operations. Pre-loaded profiles for common alloys enable one-click setup, reducing training time by 50%.
Real-time dashboards display critical metrics such as cycle time, mold temperature, and energy consumption, allowing operators to optimize processes on the fly.
Dynamic Process Control:
Closed-Loop Temperature Regulation: PID-controlled heaters maintain nozzle and mold temperatures within ±1°C, eliminating thermal inconsistencies that cause defects like porosity or warping.
5-Stage Injection Profiling: Adjustable pressure curves (0-200 MPa) accommodate materials with varying viscosities, such as zinc alloys for door handles or copper for electrical connectors.
Programmable Flexibility:
OMRON’s NJ-series PLC stores up to some custom recipes, enabling rapid transitions between product batches. For example, switching from automotive brake calipers to medical device housings takes under 5 minutes.
Automatic fault logging and root-cause analysis reduce troubleshooting time by 35%, with error codes displayed in plain language.
2. Operator Safety and Ergonomic Design
The Automated High-Pressure Casting System prioritizes workplace safety without compromising efficiency.
Low-Voltage Safety Compliance:
24V DC control circuits comply with IEC 60204-1 standards, eliminating risks of electric shock even in humid environments.
Emergency stop buttons and light curtains halt operations instantly if unauthorized access is detected.
Ergonomic Enhancements:
Tilt-Clamping Mechanism: A 15° tilting platen reduces mold height by 300 mm, enabling operators to load/unload parts without bending or climbing.
Adjustable Workstations: Optional height-adjustable control panels (700-1,200 mm range) cater to diverse operator statures, reducing fatigue during 8-hour shifts.
Environmental Protections:
Integrated fume extraction systems (up to 1,000 m³/h airflow) capture 95% of particulates and vapors.
3. Scalable Configurations for Diverse Needs
The Automated High-Pressure Casting System adapts to production demands through modular design and energy-efficient options.
Power and Energy Optimization:
Dual-Pump Systems: Standard on RDH200F+ models, dual pumps deliver 210 L/min flow rates for high-volume production (e.g., 10,000+ units/day of smartphone frames).
Single-Pump Efficiency: Smaller models (e.g., RDH138F) use variable-displacement pumps to cut energy use by 25% during low-demand periods.
Melting Solutions for Sustainability:
Industrial Oil Furnaces: Standard furnaces achieve 85% thermal efficiency, ideal for regions with strict emissions regulations.
Induction Melting: Optional 800 kW induction melters reduce energy waste by 30% and support recycled material inputs, aligning with circular economy goals.
Heavy-Duty Accessories:
Hydraulic Lift Tables: These platforms streamline mold handling for large components like EV battery housings.
Modular Spray Systems: Programmable sprayers apply water-based or solvent-free release agents, reducing material waste by 20% and VOC emissions by 90%.
4. Industry Applications and Performance Validation
The Automated High-Pressure Casting System excels across sectors, delivering measurable ROI.
Consumer Electronics Success:
A manufacturer of 5G router housings achieved ±0.03mm dimensional accuracy using the system’s servo-driven mold adjustment.
Energy recovery systems reclaimed 15% of hydraulic energy, reducing carbon footprint by 12 tons/year.
Parameter
Summary
The Automated High-Pressure Casting System sets a new benchmark for intelligent manufacturing, combining precision automation, operator safety, and eco-friendly operations. Its proven adaptability across automotive, aerospace, and electronics industries makes it an essential investment for manufacturers aiming to thrive in competitive, sustainability-driven markets.