Aluminum alloy melting furnace for rapid concentration of aluminum melting furnace,suitable for large-scale aluminum alloy die casting,casting products,centralized melting,with high efficiency,low loss,automatic operation and so on.
In the competitive metal casting field, high - quality casting hinges on an efficient and precise melting process. The DS series of aluminum alloy continuous melting furnaces, known as central furnaces, is engineered to meet the demands of large - scale metal die - casting, gravity casting, and low - pressure casting. These central furnaces ensure smooth production and top - notch output.
Furnace Design & Structure
The DS series features a robust design. The furnace body in the DS series utilizes imported high - quality refractory materials with a monolithic lining. This setup offers excellent thermal insulation and extends the lifespan of the central furnace. Some models can endure up to five years under normal use, reducing the replacement frequency and costs for foundries.
Heating Mechanism & Fuel Flexibility
The central furnace in the DS series is equipped with a modern heating system, such as a slow - speed infrared long - flame burner. This design evenly distributes heat in the molten aluminum of the aluminum alloy continuous melting furnace and allows for deep heat penetration. Melting losses and oxide formation are minimized, with a burning rate typically below 1.5%, far lower than traditional furnaces.
The DS series' central furnace is fuel - flexible, accepting wild flower oil gas, natural gas, diesel, and heavy oil. Foundries can choose the most cost - effective fuel, better controlling production costs for their central furnace operations.
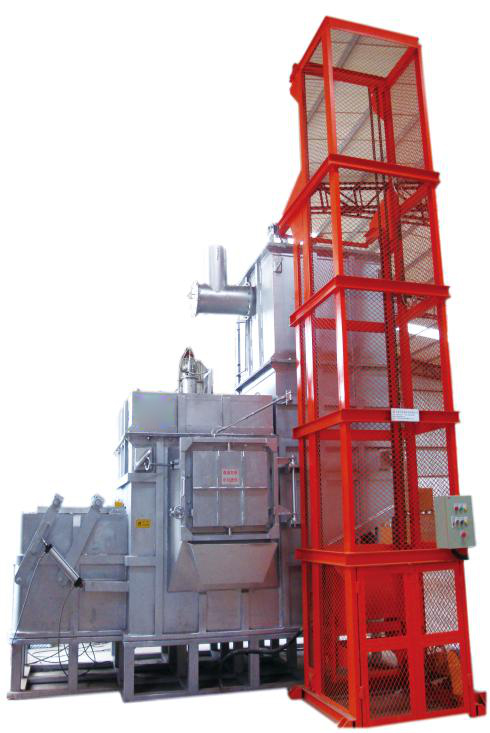
Melting Capacity & Efficiency
With a 500 - 3000 kg/h melting capacity, the DS series' central furnace is suitable for large - scale production. It can meet the needs of high - volume die - casting or large foundries manufacturing complex castings. The aluminum alloy continuous melting furnace in the DS series plays a crucial role in such scenarios.
Thanks to its advanced heating and heat transfer design, the DS series' furnace can quickly heat aluminum alloy to the melting point. Direct - contact heating elements, like ceramic ones in immersion - type models, minimize energy loss, speeding up melting and reducing energy use. This makes the central furnace eco - friendly and cost - effective.
Temperature Control & Process Automation
Stable temperature is essential for quality castings. The DS series' central furnace uses an advanced temperature control system with a PLC and PID controller. This enables accurate temperature adjustment, keeping the molten aluminum in the aluminum alloy continuous melting furnace at the optimal temperature during melting and holding.
The aluminum alloy continuous melting furnace in the DS series offers manual and automatic feeding. Once fed, it starts melting automatically, and temperature control and holding are also automated. This reduces human error, ensures production consistency, and often eliminates the need for constant operator presence, enhancing safety and efficiency for the central furnace.
Comparison with Traditional Radiant Heating Insulation Furnaces
Traditional radiant furnaces heat molten aluminum from above, leading to uneven temperature distribution. In contrast, the DS series' central furnace, especially immersion - type models, immerses heating tubes directly into the molten aluminum of the aluminum alloy continuous melting furnace, achieving more uniform heat distribution.
Traditional radiant heating insulation furnaces have problems like slow heating, uneven temperatures, and high gas absorption and oxidation. The DS series' aluminum alloy continuous melting furnace overcomes these with its innovative design, improving casting quality, production efficiency, and cutting operating costs for the central furnace.
Main Parameters
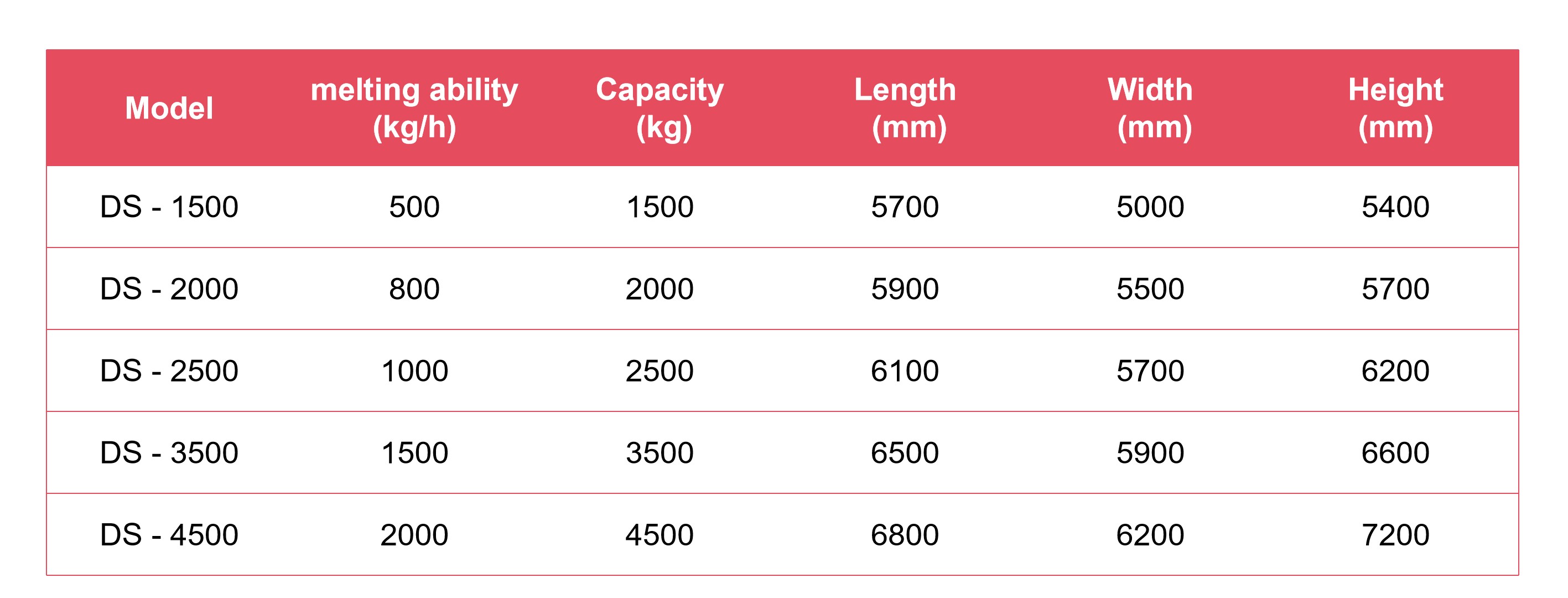
In summary, the DS series of aluminum alloy continuous melting furnaces (central furnaces) provides a comprehensive and excellent solution for aluminum alloy melting in the metal casting industry. Its advanced features and fuel flexibility make it an ideal choice for foundries aiming to optimize processes and stay competitive.