In the die casting production process, the spraying process is a crucial link to ensure mold life and casting quality.
Our automatic die casting spray machine, with advanced technologies and user-friendly designs, completely revolutionizes the traditional spraying operation mode, creating an efficient, precise, and intelligent spraying solution for die casting enterprises. Whether it’s about improving production efficiency or ensuring casting quality, this equipment can serve as a reliable assistant in the die casting production line.
1. Product Overview: Redefining the Die Casting Spraying Process
The automatic die casting spray machine is specifically designed for die casting production, achieving fully automated operation in the spraying process. It closely matches the production rhythm of die casting machines, accurately executing each link from spraying position adjustment to spraying time control, bidding farewell to the instability and inefficiency of manual operations. Suitable for various specifications of die casting machines, it is widely applied in die casting scenarios such as automotive parts, 3C electronics, and industrial machinery, constructing an intelligent and reliable production system for enterprises.
The automatic die casting spray machine completely eliminates manual operation, closely integrating with die casting machine production. After the die casting machine completes the production cycle, the equipment immediately responds and automatically executes the spraying process, ensuring timely and uniform spraying of the mold. This automated mode improves production efficiency, reduces manual errors, and perfectly synchronizes spraying with die casting production, guaranteeing process continuity.
The Y-axis drive motor adopts servo control technology to achieve precise displacement control. It can easily handle both fast movement and precise positioning. The flexible adjustment of the spraying position enables precise coverage of key areas according to the mold structure, enhancing the spraying effect and laying a foundation for high-quality castings.

Equipped with an automatic lubrication system, it regularly lubricates key components, reducing mechanical wear and extending the equipment’s service life. Compared with the frequent manual lubrication of traditional equipment, this system reduces maintenance costs and workload, ensuring the equipment always operates at its best.
It provides two choices: nozzle type and copper tube nozzle. Users can freely select according to production processes, mold types, and the characteristics of spraying media. Whether it’s fine spraying for small molds or large coverage spraying for large molds, the equipment can meet the requirements of different scenarios through flexible nozzle configurations.
Adopting Mitsubishi PLC programming control endows the equipment with intelligent attributes. Preset programs can automatically memorize production parameters, and one-click calling simplifies operations. The stable control system ensures that complex spraying path planning and time control can be easily completed, demonstrating the advantages of intelligent production.
The electrical box panel visually displays functions and parameters, making the operation simple and easy to understand. The equipment is equipped with a fault code display function, which instantly prompts the cause of the fault in case of an anomaly, shortening the maintenance time, reducing downtime losses, and ensuring continuous production.
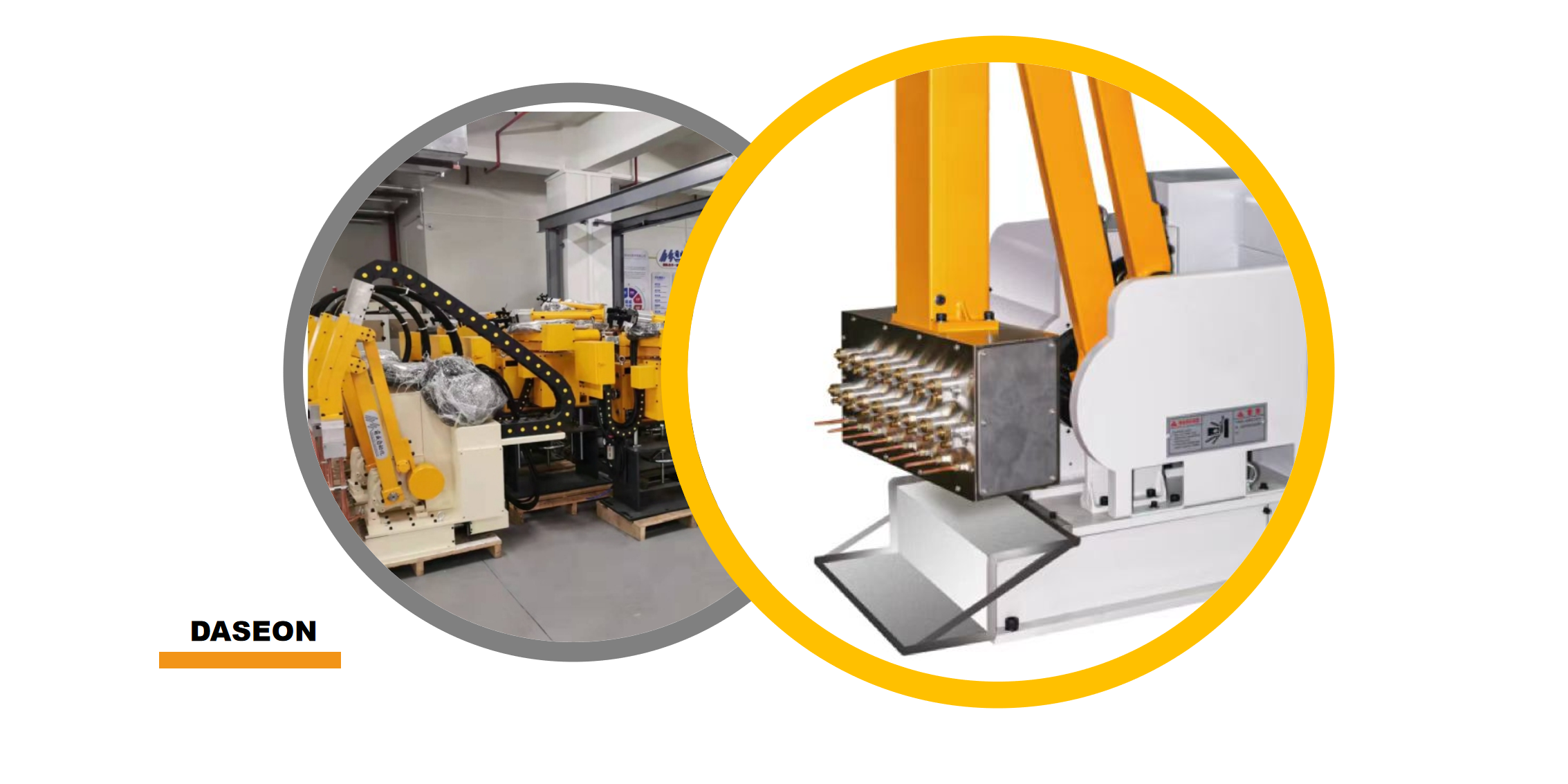
The automatic die casting spray machine offers models such as PW-01, PW-02, PW-04, adapting to different specifications of die casting machines:
PW-01: Suitable for 160T–200T die casting machines, with 12 pcs of fixed/active mold nozzles each, and a mold adjustment range of 0–400mm, meeting the needs of small die casting machines.
PW-02: Adaptable to 280T–400T die casting machines, with 15 pcs of fixed/active mold nozzles each, and a mold adjustment range of 0–650mm, handling the spraying of medium-sized molds.
PW-04: Suitable for 600T–800T die casting machines, with 22 pcs of fixed/active mold nozzles each, 3 atomizers, and an atomizing head width of 480mm, specifically designed for large die casting machines.
The air pressure source uniformly adopts 4.5–6.5kgf/cm² to ensure stable spraying pressure; the maximum spraying time for both fixed and active molds reaches 99 seconds, flexibly controlling the duration; the release agent water adjustment function supports free adjustment of water volume for both fixed and active molds, adapting to different processes.
With excellent performance, the automatic die casting spray machine is widely applied in:
Automotive Manufacturing: In the die casting of automotive aluminum alloy parts, precise spraying protects the mold, improves the surface quality of castings, and reduces subsequent processing.
3C Electronics: For the die casting of precision electronic components, it achieves fine spraying, ensuring mold forming accuracy and meeting high-standard requirements.
Industrial Machinery: During the die casting of large industrial machinery parts, large-coverage spraying protects the mold, extends mold life, and reduces costs.
Parameter
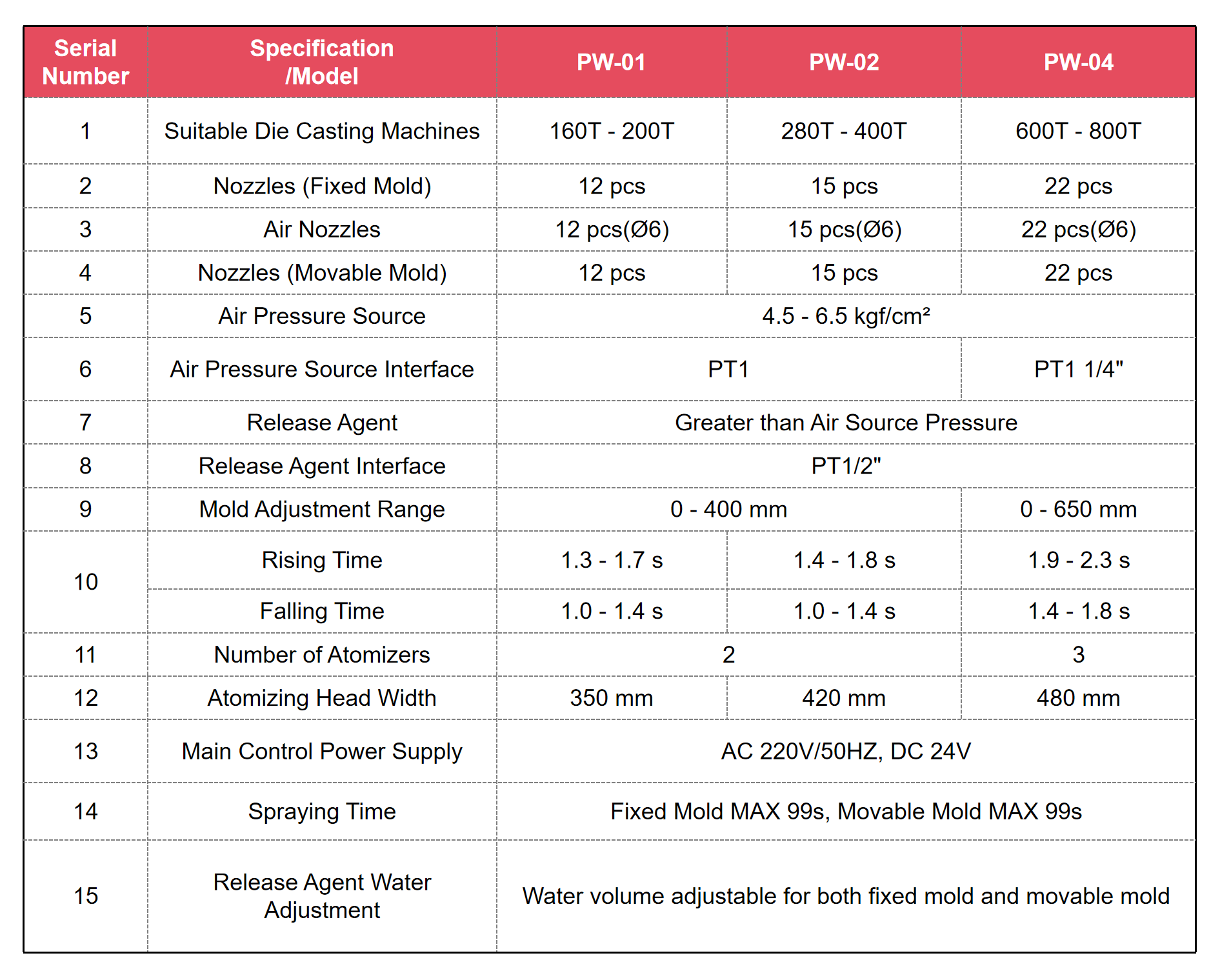