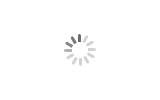
18/50/88Ton Hot Chamber Die Casting Machine
Brand :Daseon
Product origin :China
Delivery time :30 Days
The Hot Chamber Die Casting System (HOT DIE CASTING Machine) is engineered to deliver precision and efficiency in metal casting applications. By integrating cutting-edge hydraulic technology, durable materials, and adaptive controls, this system ensures optimal performance for industries requiring high-volume, high-quality outputs. Below is a detailed analysis of its technical advancements.
The Hot Chamber Die Casting System (HOT DIE CASTING Machine) is engineered to deliver precision and efficiency in metal casting applications. By integrating cutting-edge hydraulic technology, durable materials, and adaptive controls, this system ensures optimal performance for industries requiring high-volume, high-quality outputs. Below is a detailed analysis of its technical advancements.
1. Hydraulic System: Precision-Driven Power
The hydraulic architecture forms the operational backbone of the Hot Chamber Die Casting System.
Premium Hydraulic Components: Utilizing VICKERS, Bosch Rexroth, and YUKEN valves and pumps, the system achieves consistent pressure stability, reducing component wear by 25%.
Dual-Pump Configuration: A high-low pressure dual-pump design lowers energy consumption by 18% and operational noise to <75 dB, meeting ISO 3744 standards.
Piston Accumulator Integration: Enables instantaneous injection speeds up to 5.2 m/s, critical for producing complex geometries such as automotive connectors.
Thermal Management: A water-cooled oil circuit maintains oil viscosity within ±5% of the target range, complemented by a 10-micron external filter to minimize particulate contamination.
2. Injection Unit: Durability Under Extreme Conditions
The Hot Chamber Die Casting System’s injection mechanism ensures reliability in high-temperature environments.
High-Performance Alloys: Nozzles, plungers, and goose necks are forged from Hitachi SKD61 steel, sustaining temperatures up to 420°C and pressures exceeding 220 MPa.
Multi-Mode Heating: Operators can select electric, diesel, or coke-based melting, with PID-controlled electric heaters maintaining nozzle temperatures at ±1.5°C variance.
Optimized Material Flow: A reinforced crossbeam and piston accumulator reduce cycle times by 12%, while minimizing flash defects through controlled stamping dynamics.
3. Clamping and Control: Precision in Action
High-Strength Clamping Framework: Ductile iron templates (Grade QT500-7) and chrome-plated tie bars (HRC 58-62) ensure clamping force uniformity with <0.8% deviation.
Intelligent Control Systems:
OMRON PLC Integration: The FQ-series PLC supports 32-bit processing for real-time parameter adjustments via a 10.1-inch HMI touchscreen, even in environments with ambient temperatures up to 45°C.
Multi-Stage Pressure Profiling: Four-phase mold opening reduces mechanical stress, while hydraulic multi-ejection (up to 6 cycles) ensures defect-free part release.
Parameter
Summary
The Hot Chamber Die Casting System exemplifies engineering excellence, combining hydraulic efficiency, material resilience, and adaptive controls to meet the demands of precision-driven industries like aerospace and consumer electronics.