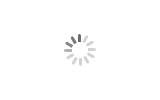
Release Agent
Brand :Daseon
Product origin :China
Delivery time :30 Days
1.Release Agent
(1)Standard Aluminum Alloy Release Agent
Product Name: Aluminum Alloy Release Agent (Demolding Agent)
Dilution Ratios: SP-618SGS (1:300) / SP-518SGS (1:200)
Appearance: Milky-white liquid
Density: 0.97–1.0 | pH: 6–8 | Thermal Stability: 360–370°C | Shelf Life: 12 months
Engineered with imported additives, this release agent ensures effortless demolding and post-treatment cleanability. It resists copper tube adhesion, reduces carbon buildup, and enhances mold longevity while delivering bright, defect-free surfaces. Certified for low VOC emissions (SGS, MSDS, VOC compliance), it prioritizes operator safety with minimal fumes and odor.
The formulation combines specialized release compounds, surfactants, and anti-corrosion agents for instant emulsification. High dilution ratios, coupled with thermal resilience and gloss enhancement, elevate die-casting efficiency, component quality, and mold durability.
(2)High-Performance Aluminum Alloy Release Agent
Product Name: Aluminum Alloy Release Agent (Demolding Agent) [Enhanced]
Dilution Ratio: SP-718SGS (1:300) | Thermal Stability: 390–400°C
Appearance: Milky-white liquid
Density: 0.97–1.0 | pH: 6–8 | Shelf Life: 12 months
This premium release agent excels in high-temperature die-casting environments, preventing mold adhesion and carbon deposits for extended tooling life. Its optimized formula ensures pristine surface finishes and easy post-processing. Certified (SGS, ESDS, VOC) for eco-compliance, it minimizes workplace hazards with low smoke and odor emissions.
Formulated with advanced additives, surfactants, and gloss enhancers, it achieves rapid emulsification and superior film stability. The high dilution ratio and unmatched release performance enhance productivity, component consistency, and cost-efficiency in demanding applications.
(3)Zinc Alloy Release Agent
Product Name: Zinc Alloy Release Agent (Demolding Agent)
Dilution Ratio: ZP-318SGS (1:200)
This advanced release agent utilizes imported additives and proprietary formulations to ensure superior demolding performance without compromising post-processing efficiency. It prevents mold adhesion, eliminates surface blackening, and withstands high-temperature die-casting environments. As an eco-friendly solution, it features low odor and minimal fume emissions, ensuring a safer workspace. Enhanced cleanability reduces residue buildup, improving product quality.
Formulated with specialized release additives, surfactants, corrosion inhibitors, and gloss enhancers, this release agent emulsifies instantly upon dilution. It delivers consistent high-temperature resistance, optimal surface brightness, and extended mold lifespan. Its high dilution ratio and exceptional release efficiency significantly boost die-casting productivity and component quality.
(4)Magnesium Alloy Die-Casting Release Agent
Product Name: Magnesium Alloy Release Agent (Demolding Agent)
Dilution Ratio: ZP-818SGS (1:100)
This release agent forms a continuous protective film on die surfaces, facilitating smooth part ejection and rapid mold cooling to shorten cycle times. Selecting the appropriate magnesium alloy release agent requires adherence to critical criteria:
Optimize dilution ratios, spray volume, and air-blowing parameters to maintain film integrity.
Prioritize formulations with minimal mold abrasion.
Avoid excessive wax content to prevent residue accumulation.
Match agent properties to part geometry (e.g., thin-walled precision components).
Magnesium alloys exhibit low mold affinity, fast solidification, and significant shrinkage, necessitating precise control over release agent compatibility. Contamination risks in recycled materials and stringent surface treatment requirements (e.g., rust prevention, coating) further underscore the need for residue-free performance.
2.Iubricating Particles
(1)Product Benefits:
·Eliminates contamination from traditional oil-based lubricants.
·Minimizes porosity formation in castings.
·Triples the service life of die-casting plungers compared to pure oil lubrication.
·Delivers clean, oil-free surfaces with high brightness.
·Boosts injection speed for enhanced productivity.
·Enables clean recycling of sprues, runners, and biscuits—free of residue, smoke, or environmental impact.
·Removes wastewater disposal needs and eliminates water-cooling systems or shot sleeve cleaning.
·Reduces consumption rates for cost efficiency.
·Improves workplace safety.
·Maintains factory cleanliness (floors, ceilings, equipment), aligning with eco-friendly standards.
(2)Lubricant Granules :
Available in two variants: graphite-infused and graphite-free. Granule size options:2.5–2.0mm diameter,2.0–1.5mm diameter,1.5–1.0mm diameter.
These granules melt instantly upon contact with the shot sleeve and plunger tip. Leveraging advanced capillary action, they form a high-performance lubricating film. No complex dispensing systems (e.g., pumps or sprays) required—ideal for streamlined operations.
(3)Storage Instructions:
·Store in a cool, dry indoor area; avoid heat exposure.
·Shelf life: 12 months | Packaging: 25kg/bag
3.Plunger Head
4.Coating Agent (Crucible Coating)
This concentrated coating agent requires mixing at a 1:2 ratio (1 kg coating agent : 2 kg oil).Designed to protect crucibles, ladles, and other tools exposed to molten alloy.Molten alloy processing temperatures can reach ~800°C. During melting, holding, or transferring, the alloy and its oxides corrode equipment such as crucibles, ladles, and casting channels. This coating agent extends tool lifespan by:
·Preventing contamination of the alloy from impurities (e.g., iron).
·Reducing harmful gas emissions during smelting.
·Forming a dense, corrosion-resistant protective layer.
(1)Primary Applications:
Protective coating for : Crucibles, ladles, slag skimmers;Thermocouple sheaths;Cores and pins.
(2)Key Benefits:
Minimizes alloy contamination and impurity penetration.Delays corrosion of tools exposed to molten alloy.Enhances operational safety and tool durability.
(3)Usage Instructions:
·Mixing: Blend the coating agent with oil at a 1:2 ratio until uniform.
·Preparation: Clean the tool surface and preheat to ~100°C.
·Application: Apply evenly with a brush.
·Curing: Dry the coating using a low flame to activate flow-enhancing components, ensuring a dense and robust protective layer.
·Effectiveness: The coating remains stable for ~24 hours post-application.
5.Aluminum Slag Remover
(1) Application Method:
Post-refining : Evenly sprinkle the powder over the slag surface.Stir immediately to pulverize the slag.Remove the slag powder after disintegration.
As a Covering Agent : (A)First application: Add during initial melting.(B)Second application: Add after full melt.(C)Third application: Add post-refining to enhance slag-aluminum separation.
(2) Details
6.Other Consumables
-
Download
- SGS ENG..pdf
- VOC ENG..pdf